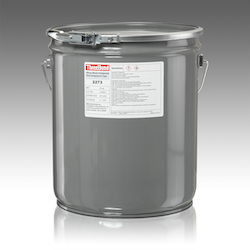
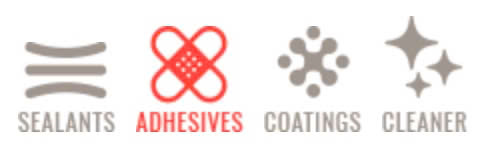
2200 SERIES
INDUSTRIAL EPOXY RESINS
USAGE
These ThreeBond adhesives use industrial epoxy resin as their main component. They are excellent for a myriad of purposes including general purpose adhesion and sealing, and for electronic device bonding, filling, repair, casting and impregnation. Epoxy resins, also known as polyepoxides, are reactive prepolymers and polymers which contain epoxide groups. They often have favorable mechanical properties and high thermal and chemical resistance which make them ideal for a variety of industries and applications.
Many people choose industrial epoxy resins because they are familiar, especially for various applications. We most often see industrial epoxy resins being used in the following industries:
• Automotive
• Automotive electronics
• Consumer electronics
• EV and fuel cell manufacturing
With a large array of different types of epoxy resins readily available, our selection allows us to serve our customers’ every need. With black and white options, varying degrees of viscosity and lap shear strength, our industrial epoxy resins suit every job.
WHY CHOOSE THREEBOND INDUSTRIAL EPOXY RESINS?
As a business owner, you understand the importance of choosing the right supplies and materials the first time around. With such a huge selection of industrial epoxy resins, you can easily find solutions that will help to reduce overhead costs, reduce process steps, simplify the overall workflow and eliminate waste. We know that every dollar matters when it comes to working efficiently and we are here to be the partner you need to find the right solutions for every job.
It doesn’t take long to see how our industrial epoxy resins are uniquely designed to meet the high standards of our varying clients. From the automotive industry to consumer electronics, our industrial epoxy resins are designed to exceed your expectations and improve your workflow.
Use our data sheets below to help you find the perfect industrial epoxy resins for your application.
PRODUCT SPECIFICATIONS
Product Name | Features and Uses | Color | Viscosity (Pa·s) | Lap Shear Strength (MPa) | Hardness | Tg (°C) | Thermal Conductivity (W/m·K) | Curing |
---|---|---|---|---|---|---|---|---|
TB2202 | Low-temp cure, trigger type; excellent adhesive & heat resistance | Black | 13 | 10 | D88 | 105 | – | 60 °C × 180 min; 70 °C × 50 min; 70 °C × 20 min |
TB2204 | Low-temp cure, trigger type; excellent adhesive & heat resistance | Black | 28 | 13 | D89 | 105 | – | 60 °C × 180 min; 70 °C × 50 min; 70 °C × 20 min |
TB2206 | Low-temp cure, trigger type; excellent adhesive & heat resistance | Black | 100 | 15.7 | D87 | 107 | – | 60 °C × 180 min; 70 °C × 50 min; 70 °C × 20 min |
TB2206B | Low-temp cure, trigger type; excellent adhesive & heat resistance | Black | 140 | 17.7 | D89 | 102 | – | 60 °C × 180 min; 70 °C × 50 min; 70 °C × 20 min |
TB2206S | Low halogen content, heat-curable epoxy resin | Black | 15 | 12 | D87 | 106 | – | 80 °C × 30 min |
TB2222P | Solder heat‑resistant, high peel, thermal shock resistant | Black | 45 | 24 | D89 | 115 | – | 100 °C × 60 min |
TB2235L | High Tg, high storage modulus, heat‑curable | Black | 80 | 23 | D92 | 150 | – | 140 °C × 30 min |
TB2237J | High Tg/modulus, heat‑curable; good adhesion | White | 115 | 26 | D89 | 150 | – | 120 °C × 60 min |
TB2249G | Heat‑curable, high shear & peel strength | Black | 75 | 39 | D90 | 104 | – | 160 °C × 30 min |
TB2249K | Heat‑curable, high-strength, structural bonding; oily surface use | Black | 880 | 34.6 | D81 | 118 | – | 130 °C × 30 min |
TB2270J | High heat dissipation; low expansion & shrinkage | White | 150 | 9 | D96 | 117 | 4.2 | 100 °C × 40 min |
TB2272F | UL94 V‑0 flame‑retardant, heat‑curable | Black | 75 | 21 | D92 | 117 | – | 100 °C × 60 min |
TB2273E | High Tg, high peel; induction-curable | White | 70 | 40 | D94 | 120 | – | 150 °C × 30 min |
TB2274 | Low-temp cure, under-fill agent for CSP/BGA | Black | 12 | 11 | D86 | 65 | – | 70 °C × 50 min |
TB2274C | Low-temp cure, under-fill for CSP/BGA | Black | 12 | 16 | D83 | 80 | – | 85 °C × 60 min |
TB2285 | High heat resistance, high Tg; motor coil impregnation | White | 120 | 20 | – | 163 | – | 120 °C × 60 min |
* Measurements are taken under the standard testing conditions for each grade.